Beyond the HIER 30-Slide Barrier
The adoption of heat induced epitope retrieval, or HIER, as a standard enhancement technique for IHC has framed the use of IHC as a valuable tool for the examination of formalin fixed, paraffin embedded (FFPE) tissue for the past few decades.1 The mechanical requirements of heat induced epitope retrieval protocols framed the maximum performance features of automated IHC staining instruments in recent years as well. Those constraints have limited the throughput capabilities of automated IHC staining platforms, until now.
As the name implies, heat induced epitope retrieval (HIER), also known as Antigen retrieval, is driven by the application of sustained heat and specially formulated buffers to glass slides and the affixed FFPE tissue. The high, sustained heat required for the HIER process can be generated by manual methods such as steamers, heat baths, microwave ovens, or pressure cookers.2 For automated IHC instruments that support on-board HIER, indirect heat applied by under-slide heaters are commonly employed to provide the sustained high temperatures required for the HIER process.3 However, the physics of generating and maintaining high temperatures across dozens of slide heaters in parallel imparts significant electrical demands on the power supply for the instrument. The maximum power draw from standard laboratory wall outlets (typically 1800W) imposes a threshold to the heat output that any given instrument can sustain for an extended period of time (Red section Figure 1).
Figure 1: Power usage of current Automated IHC Staining Platforms

Laboratories using automated IHC staining equipment have become accustomed to this HIER processing limit in the form of a “30-slide barrier;” in other words, the lack of enough input power to apply high heat to more than 30 slides at once. Many IHC labs prefer the workflow advantages of automated staining, including on-board automation of the HIER process. However, the 30-slide barrier curtails those advantages by limiting the parallel processing of slides and ultimately impacting the overall daily slide throughput of the laboratory. To break the 30-slide barrier, a new approach to the power management of the automated HIER process was required.
In a recent article, Dr. David Basiji outlines how a rechargeable Lithium Ion Battery can be used to store extra input energy for automated IHC protocols, boosting the parallel slide processing capability for HIER, then recharge when the IHC protocol’s power demands are low (Figure 2).
Figure 2: Power usage of Automated IHC Staining Platform with Hybrid Lithium Ion Power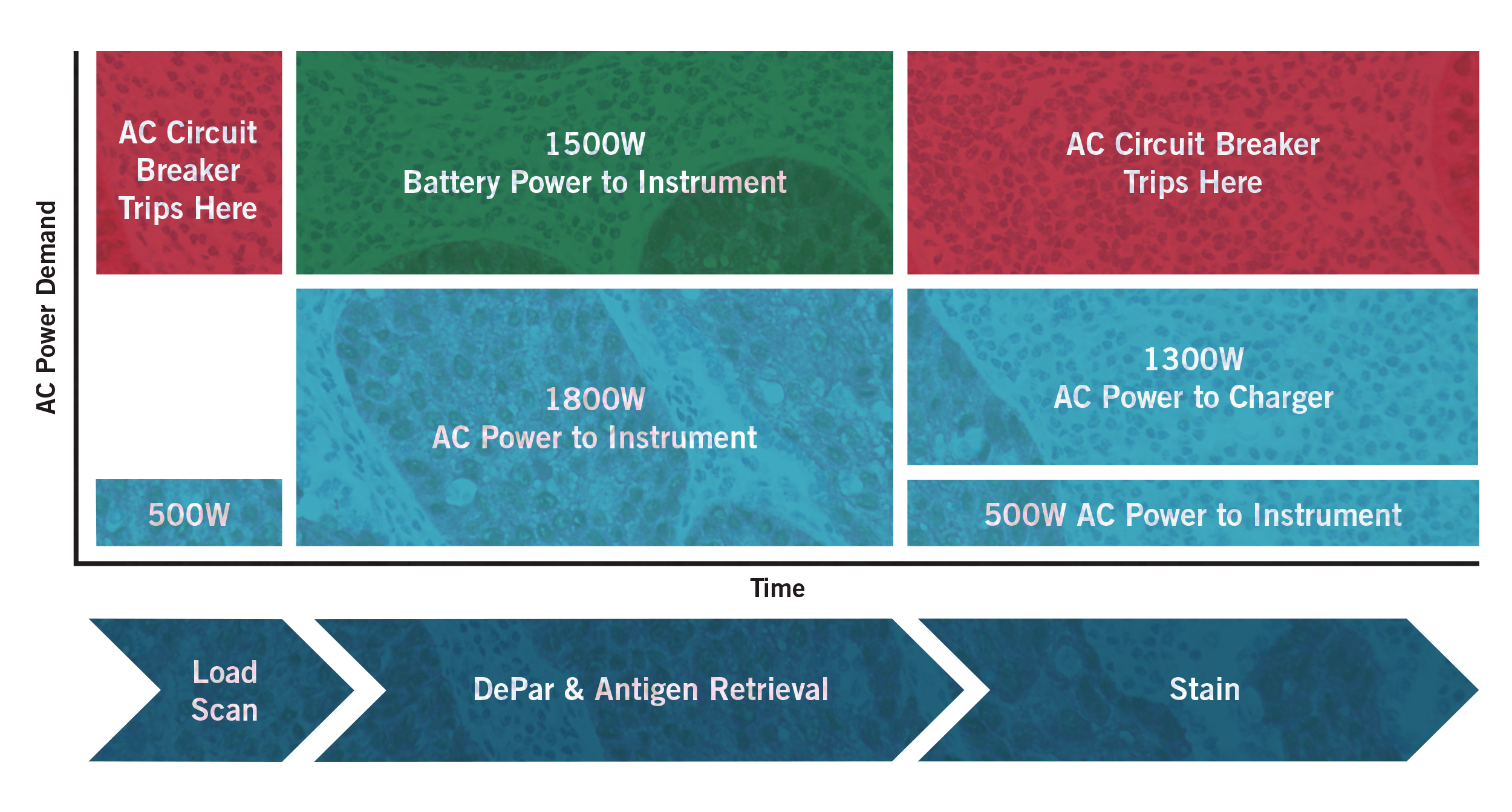
Even more recently, Biocare Medical harnessed that power in the design of the new VALENT automated staining platform, a fully open, fully automated IVD staining platform for IHC laboratories. VALENT employs battery hybrid power to maximize parallel slide processing for HIER and break the 30-slide barrier, providing laboratories with unparallel throughput for automated IHC applications.
For a more detailed explanation of how to break the 30-slide barrier with Biocare’s new VALENT platform, learn more about the Power of Advanced Automation.
References: 1. Shi, SR et al book: “Antigen Retrieval Immunohistochemistry Based Research and Diagnostics.” 2. Ramos-Vara JA, Miller MA. Vet Pathol. 2014 Jan;51(1):42-87. 3. Prichard JW. Arch Pathol Lab Med. 2014 Dec;138(12):1578-82.